As Dubai Marina continues to take
shape in the fashionable Jumeirah area of the city, Ben
Smalley talks to Yehia Abudullah of Al Habtoor
Engineering Enterprises about the company's construction
of Marina Terrace - a stunning residential tower in the
heart of the new marina development.
Dubai's decision to allow
expatriates to buy property in the emirate has fuelled a
spate of construction projects to cope with the demand
from residents and investors keen to step onto the
property ladder in the most progressive and dynamic city
in the Middle East.
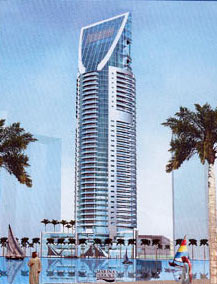
Emaar's spectacular Dubai Marina
project is just one of the pioneering new initiatives
which have caught the imagination of Dubai residents,
and Al Habtoor Engineering Enterprises is firmly
involved in the project through the construction of four
residential and hotel towers which form part of the
unique 'city within a city.'
One of these developments is Marina Terrace, a
residential tower which Al Habtoor Engineering
Enterprises is building, along with Norr Consultants, on
behalf of Damac Properties.
Project manager Yehia Abudullah
explained: "The whole Dubai Marina area from Dubai
Internet City to the Sheraton Jumeirah is being
developed by Emaar. They have sold some land to
investors such as Damac Properties, while the rest is
being developed by Emaar themselves."
With literally dozens of high-rise
buildings destined to be built around the man-made
marina next to Dubai's famous Jumeirah Beach strip,
there is great competition between developers and
construction companies to demonstrate the quality of
their work.
"Basically there will be many towers
in this area so there is a big competition between
investors to provide the best finishing of the towers,
the best rooms and the best views," Yehia said. "This
also reflects on us as the constructor, as we are in a
position to show what we can do - we are in a challenge
to show that Al Habtoor Engineering Enterprises is a
leading company, that we can achieve projects on target
without any delays - and this is a commitment made by us
all.
"There are also some clients and
contractors involved with Dubai Marina who have never
worked with Al Habtoor before, so this is a good
opportunity for us to showcase the quality and
commitment to work that we have, and also the systems
that we employ. It is also an important development for
the future of Dubai, so we are especially pleased to be
involved with that."
Marina Terrace comprises a six-storey
podium, which forms the base of the building, rising
from which is a 35-storey tower comprising the
residential components of the building - a mixture of
one, two and three bedroom flats.
The podium comprises car parking and service areas and
will be topped at the sixth level with leisure
facilities, including a swimming pool, Jacuzzi, tennis
court and sports training area.
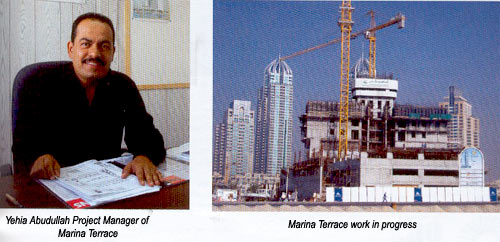
"There are also some commercial
areas, which could be used as a beauty salon or some
other purpose," Yehia said. " And there is also space
for a kids' play area on top of podium six, and there
will be a lot of landscaping in this area. In addition,
there is also a ramp, which comes up from the main
street to podium six, to provide vehicle access for
people visiting the tower to pick somebody up, or drop
somebody off."
There will be around 200 apartments
in the building and, Yehia says, all but two or three
have already been sold by Damac Properties, which
reflects the demand and popularity of the development -
especially as construction only began six months ago.
"We started on 3 September 2003 and
are due to hand over the project in April 2005 - so we
have a total construction time of 19 months," Yehia
said. "This type of project is very time constraining -
you would normally expect to take at least two years to
build a tower like this, so to build it in 19 months
creates time pressure - it is a fast-track job and it
has to be completed on time so we are pushing and
working day and night in two shifts to ensure we stay
within the programme and hand over the project on time.
"Right now we have about 550 Al
Habtoor people working on the site, but in the future
many subcontractors will also be involved, which will
increase that number further by around 200-300 people."
Working surrounded by the clear
turquoise waters of the marina provides for a
spectacular view, but the presence of so much water can
also have its problems. Yehia explained: "We had some
problems in the beginning as we have two basements which
go down about seven metres below the water level and we
are just eight metres away from the lake. So in the
beginning, we had to get the area dry for working, but
we have overcome this initial problem and are now in a
good position and ahead of the programme."
One of the ways in which Yehia and
his team are 'fast-tracking' the project is by using a
technique known as 'slip forming' in the construction of
the core of the building.
"There is a lot of concrete and
reinforcement in the core walls which takes time to
complete," Yehia explained. "So we have incorporated
this system and are always slip forming this area ahead
of the outer walls in order to minimise the time
required to construct each floor - to go from one floor
to another is much easier for us if the core wall is
ahead."
Slip forming, as the name suggests,
is a sliding-form construction method of pouring
vertical concrete structures. It begins with the
construction of a fixed-diameter form on top of a
foundation, with a back-up support and bracing system to
ensure that the form maintains its shape during
movement. Inside and outside forms create the cavity of
the wall, and inside this cavity, reinforcing steel is
tied together vertically and horizontally to reinforce
the concrete wall. The form is then connected to jack
rods with hydraulic jacks, which automatically move the
form vertically in minute increments as the concrete is
being poured. Once pouring begins, it continues until
the top of the structure is reached, allowing for a
monolithic poured concrete structure.
"This is not a new technology, but
we are fairly unique in using it here and we have had
other construction firms come along to see how we are
doing it," Yehia said.
Marina Terrace is the second project
Yehia has managed since joining Al Habtoor Engineering
Enterprises in May 2003. Previously he worked as project
manager for a contracting company in Abu Dhabi, and also
worked in Kuwait for a number of years after graduating
from the University of Texas in the USA in 1983.
His first job for the UAE's leading
construction company involved building a new grandstand
and refurbishing the existing facilities at the Al Ain
Club ahead of the UAE's hosting of the FIFA World Youth
Championships last year.
The techniques involved in building
a football stadium are vastly different from a high-rise
tower, but such is the versatility of the projects Al
Habtoor Engineering Enterprises is able to execute. And
Yehia was especially pleased to see the stadium his team
built receiving international attention during the
championships.
"Sadly, I was unable to go to a game
because I was too busy here, but I read about it a lot
in the newspapers and the tournament seemed to go very
well and everyone was happy with the facilities," he
said. "The UAE may not have won the tournament, but the
country showed it has the facilities and ability to
stage a world-class competition which will hopefully
serve as a good advert for the UAE across the world and
attract similar events in the future."
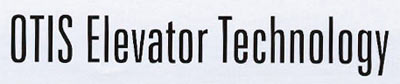
When
Elisha Graves Otis invented the elevator in 1853 his
revolutionary device enabled buildings – and architects’
imaginations – to climb ever skyward, giving a new and
bolder shape to the modern urban skyline.
The industry has come a
long way since the pragmatic American mechanic first
stunned the gathered crowds at New York’s Crystal Palace
with a demonstration of his pioneering safety brake
mechanism that enabled lifts to work without the
inherent risk of falling due to rope failure.
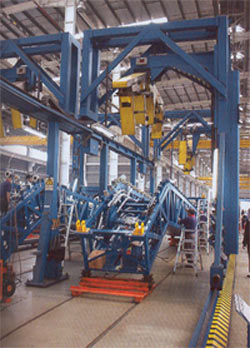
Today, more than a century
and a half later, the Otis Elevator Co. still stands as
the world’s leading company in its field, with more than
60,000 employees serving customers in nearly every
country of the world.
The United Arab Emirates
is no exception, where Otis has a proud history as the
first manufacturer to establish a presence in the
country in the late 1960s. Otis is now expanding its
market share in the UAE even further by sourcing its
market-leading elevators and escalators from Otis
factories in China, in addition to Europe.
Yusef Shalabi, general
manager of Otis in the UAE, says the Chinese factories
have enabled substantial cost savings for clients,
greater choice of product and enhanced customer service.
“Up to last year, we were
sourcing elevators from Otis factories in France and
Spain and escalators from Otis factories in Germany, but
the strength of the Euro and weakness of the dollar has
made buying from Europe prohibitively expensive,” he
explains. “Otis has four factories in China and, now
that we are sourcing our products there, we are able to
offer our valued customers in the UAE an even better
service at a greatly reduced cost.”
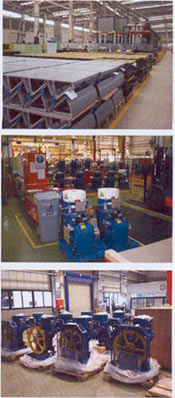
Among the benefits for
Otis customers in the UAE is an increased product range,
with the Chinese factories offering a wider variety of
models than their European counterparts, while the
ability to specify different finishes, buttons, ceilings
and floorings has eliminated the need for costly
customisation to take place in the UAE to meet specific
client requirements.
“All products are
manufactured by Otis in Otis-owned factories and come
with the Otis guarantee and warranty,” Shalabi says. “So
our customers are benefiting from a better price, even
better choice of product and better quality, which has
helped propel our sales and enabled us to be much more
competitive.”
Otis prides itself on
safety, and customers also have the added peace of mind
that comes with buying an Otis elevator, escalator or
moving walkway.
“Our products come with
the latest safety features as standard, rather then as
optional extras,” Shalabi explains. “These features are
included because Otis as a company demands them, not
because local regulations require them. Our safety
standards are second to none. This is an invisible
advantage for our clients and just one of the many
reasons why Otis is the world’s largest and most
successful elevator company in the world.”
|