After the exceptional Burj Al Arab and the elegant
Emirates Towers, Dubai now boasts yet another
spectacular landmark, the Madinat Jumeirah Resort. Quite
different in style from the above two buildings, this
property gives visitors a true feel of old-time Arabia
while combining the region’s traditional architectural
features with modern state-of-the-art facilities. With
its lively souk, picturesque canals and beautiful
waterfront, the resort has quickly become a focal point
of social life for the emirate’s residents as well as a
major attraction for an ever-increasing number of
foreign visitors.
After the
first concrete was pored on 30th July, 2002,
three days after the
Dhs.535
million (US$150 million) contract
was awarded to
the Joint
Venture between the Dubai based Al Habtoor Engineering
Enterprises and Murray & Roberts Contractors from South
Africa, the second and biggest phase of this challenging
project was completed in just 19 months. Al Shindagah
talks to Peter Fell, the JV Project Manager of Madinat
Jumeirah about this spectacular new development.
Phase two
of the development
included
the eight-storey Al Qasr Hotel, which is reminiscent of
an opulent summer palace. Spreading onto a built area of
58,000 square metres, the five-star hotel boasts 296 rooms and suites,
restaurants and lounges, business facilities and car
park for over 200 cars.
Part of
phase two are also 29 villas with 284 rooms
and suites,
as well as
The Royal Villa, which is essentially a beachside palace
with elaborate designs and finishes. The HMR JV was also
responsible for building the complex’s
spa, which features 14 small stand-along buildings and
28 private treatment rooms and spreads to a built-up
area of 4,400 square metres. The contract also included
work on restaurants, swimming pools, landscaping and
roads as well as a
corporate
office building for Jumeirah International, which is the
hotel operator for the Madinat complex.
A main
feature of the whole development is a network of
man-made water canals and lagoons with some 60,000 cubic
metres of pumped water circulating in them at any given
moment, which was also part of the scope of work of the
Joint Venture. Almost four kilometres in length, and
featuring 17 bridges, as well as a 24-metre long main
bridge at the entrance, the canal system is one of the
development’s most attractive features with hotel guests
going around its parts via traditional abrah boats.
Aiming to
provide an authentic experience, the project reproduces
traditional elements from old buildings in Dubai’s
Bastakiya region. The buildings’ attention to detail is
what contributes to their charm and it was precisely
this feature that posed one of the main construction
challenges for the developer.
“The
extremely elaborate detailing in the mosaics and the
intricate panelling meant that a large number of
labourers skilled in the region’s traditional
construction methods needed to be sourced and hired.
Traditional methods were employed on a huge scale with
labourers placing over 135,000
cubic metres of concrete, 35,000 cubic metres of plaster, some three million
masonry blocks and 100,000 square metres of ceramic
finishes”, explained Peter Fell.
Safety and
quality control was a major concern for the contractor
with some 3,500 varies inspections and over 1,000
compaction tests being performed in the course of the
project. The Quality control team also produced 10,000
concrete test-cubes and checked more than 20,000
delivery mixer trucks to verified quality of supplied
concrete and plaster.
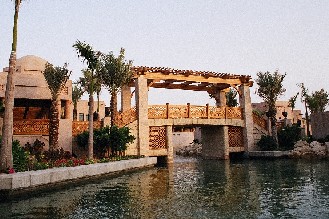
“With only
19 months allocated for the project, the time factor was
another major challenge for the contractor. The time
constraints meant the contractor had to be as efficient
as possible in managing both workers at the site and
subcontractors. With about 4,000 workers on the site
during peak times and with some 200 subcontractors, the
project was a huge management exercise”, Fell said.
“The site
was so big that on the average, supervisory staff would
walk a minimum of five kilometres a day,” continued
Fell. “Work days were 11 hours long
with the
site being effectively in operation throughout the week.
The project was an elaborate logistics exercise as the
canal network meant the contactor had to overcome
difficulties in accessing the artificial islands, which
are part of the project. Moreover, construction was
taking place during an upgrading of the road network
surrounding the project.
“Working
smart was just as important as working hard and one way
to make sure all work was streamlined and tight
deadlines were kept, was to divide the whole job into
two major sections comprising of the Al Qasr hotel and
the villas with different teams, working on probably
five or six fronts at one and the same time. The project
required a team of 18 management staff and 27
engineers.”
According
to Fell, the
cooperation between the HMR
team and the consultant also played a huge role in the
success of the project. “Everybody worked towards the
same goal – to get the project finished on time,” he
said.
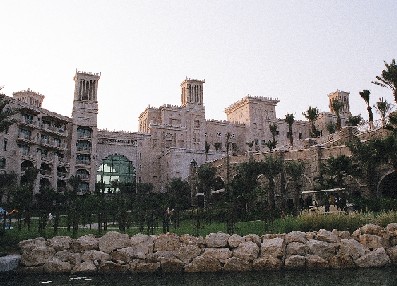
The team
consisted of project managers Mirage Millé Leisure and
Development Inc, South Africa-based DSA Architects
International and interior designers KCA International
Designers, well-known in Dubai for their work on the
Burj Al Arab and Emirates Towers projects.
As the
design was produced in South Africa, the contractor had
to liaise with DSA electronically to obtain 16,000 drawings and produce 260,000 copies needed for work on the project.
“In the
initial stages we went through quite a stringent
interviewing process with the consultants,” Fell said.
“We had the key people approved before the contract was
awarded and this also helped us all work better
together.” According to Fell, one of the main reasons
why his team has been awarded the contract was because
it consisted of the right people.
The joint
venture with Al Habtoor Engineering, one of the leaders
in the local market, was another decisive factor. “The
team over at Al Habtoor Engineering has an incredible
understanding of the local market and of the way things
are done here,” Fell said.” Our partners have a
substantial labour force and this allowed us to recruit
and employ additional labour as and when required.
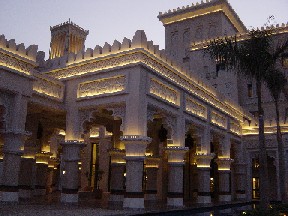
Unlike many other companies, who might form a joint
venture only for the sake of a specific project, the
partnership between Al Habtoor Engineering and Murray &
Roberts dates back to 1994. The Joint Venture mechanism
seems to be working excellent for the two partners who
have accumulated an impressive client portfolio,
including some of the most technologically-advanced and
visually attractive building throughout the country. The
Al Habtoor Engineering /
Murray & Roberts Joint Venture boasts developments such as the
Burj Al Arab hotel, the Sheikh Rashid Terminal at Dubai
International Airport and the Shangri-La hotel, as well
as Sharjah’s City Centre and Marina Mall in the capital
Abu Dhabi.
“A lot of
our success in the country is because we are and have
always been in a joint venture agreement with Al Habtoor
Engineering,” Fell said. “Throughout the years we have
jointly developed systems and methods of work to make
sure we deliver consistently good results,” he said,
adding, “All our quality and safety procedures are the
same, we know each other and we work exceptionally well
together.” |